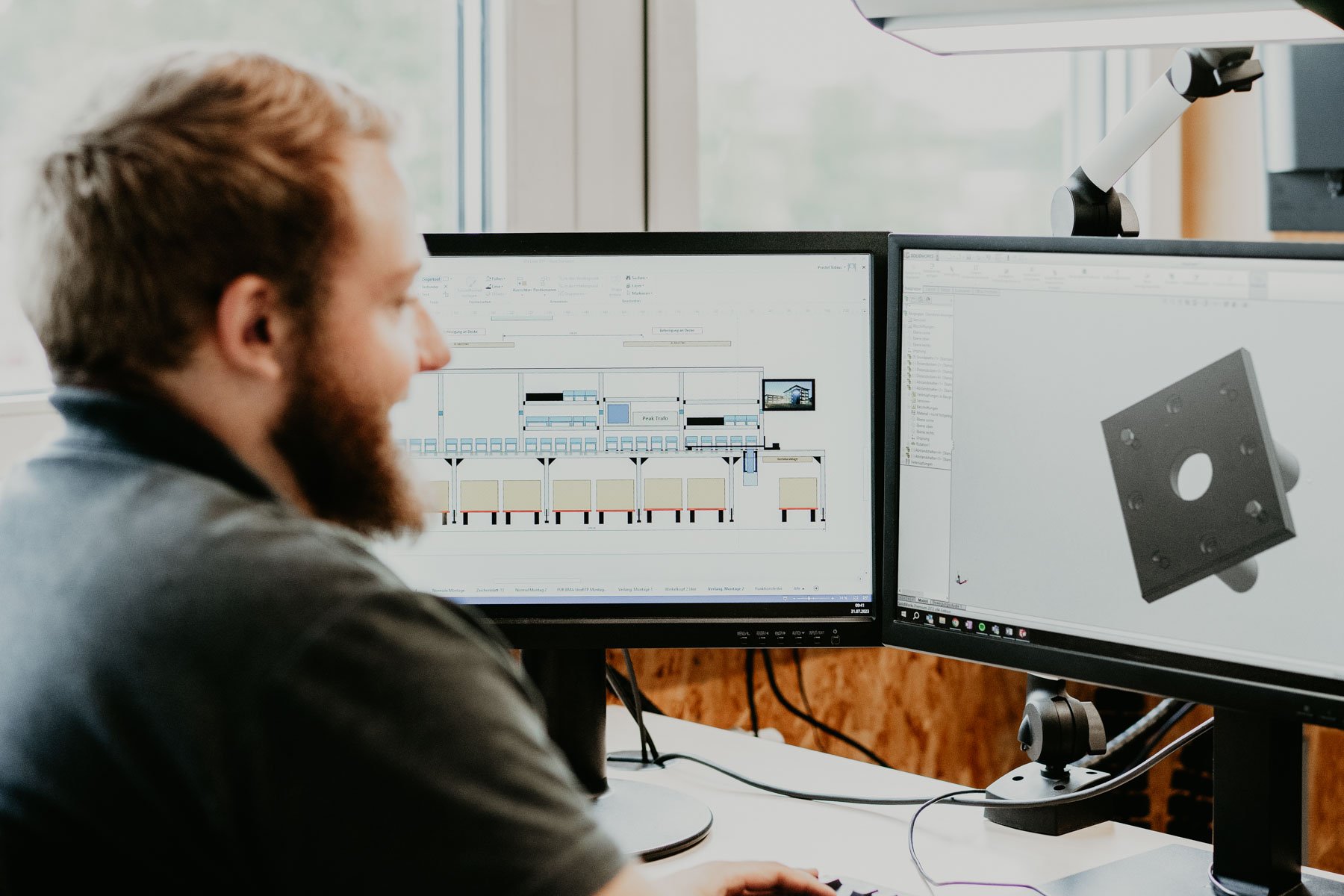
Interface measurement overview
Interface measurement is a method for determining the interface between two different phases or materials in a container or pipe. This type of measurement is of great importance in various industrial applications and processes, especially when it comes to monitoring and controlling the level of liquids or bulk solids in containers or pipes. Typically, the interface between liquids or liquids and solids is measured:
INTERFACE MEASUREMENT OF LIQUIDS
This is particularly relevant when two liquids of different density, viscosity or composition are present in a container or tank and it is important to accurately detect and monitor the transition point between them. Sensors are used to detect the transition point between the two liquids and enable precise measurement of the distance between the sensor and the interface. The data obtained can then be used to control processes or to prevent mixing or contamination in industrial applications, for example in the food industry, the chemical industry or environmental technology. Interface measurement is an important technique for ensuring quality and safety in various applications.
INTERFACE MEASUREMENT OF SOLIDS IN LIQUIDS
Solid substances in liquids and sludge levels are usually collected in sediment tanks, filters or lamella separators. Typical areas of application can be found in the metal industry, chemical plants, lime or gravel works and the waste water sector. Interface measurement of solids in liquids is an important technique for monitoring the level of solids in a liquid or their sedimentation in a tank or pipe.
Measuring methods for interface measurement
There are different methods for interface measurement, the choice of which depends on various factors, including the type of material, process conditions, accuracy requirements and cost. Interface measurement is of great importance in numerous industries such as chemicals, food production, water and wastewater treatment, oil and gas, and many others in order to operate processes efficiently and safely. Depending on the industry, different project planning options are suitable for continuous measurement and level detection.
- Capacitive interface measurement: This method measures the capacitance of a capacitor located near the interface. The capacitance changes depending on the properties of the materials on both sides of the interface. This change in capacitance is converted into an electrical signal and used for level measurement.
- Ultrasonic based interface measurement: In this method, ultrasonic waves are emitted from a transmitter in the direction of the interface. The waves are reflected by the interface and detected by the receiver. The transit time of the ultrasonic waves is measured to determine the distance to the interface and thus the fill level.
- Radiometric interface measurement: This method uses radioactive isotopes to measure the density of the materials in a container. The attenuation of the radiation by the materials is measured in order to draw conclusions about the interface and the fill level.
- Float interface measurement: A float that is lighter than one phase and heavier than the other phase is inserted into the container. The float is positioned at the interface and thus indicates the fill level.
- Radar and laser interface measurement: These methods use electromagnetic waves (radar) or laser beams (laser) to measure the distance to the interface. The transit time of the signals is used for level measurement.
- Electromechanical interface measurement: Mechanical sensors that are inserted into the container are designed to physically touch or be in contact with the interface. Electrical signals are generated when the sensor reaches the interface and these signals are used for level measurement.
In interface measurement, UWT has specialised in capacitive, electromechanical and radar-based measuring principles, among others. Their typical areas of application are in the food industry for separating oil and water, in the chemical industry for separating various chemicals, in environmental technology for monitoring layers in clarifiers and in the petrochemical industry for separating various liquids in storage tanks. The data collected from the interface measurement can be used to activate control and automation systems to maintain the interface or to prevent unwanted mixing or contamination. Interface measurement requires high accuracy as it detects the transition between two different media. Sensors to be used should also have adjustable sensitivity, a robust design and be insensitive to contamination and moisture. Therefore, specially developed sensors and technologies are used to ensure accurate results. It is also possible to integrate the measuring devices into different control or monitoring systems.
Exemplary applications for interface measurement:
Precise interface measurement of different solids in liquids
Separation layer detection during the measurement of stone reclamation sludges
White Paper: MULTITALENT TDR IN SOLIDS & LIQUIDS
What should you look out for
when choosing the right interface measurement?
Choosing the right interface measurement depends on various factors, including the type of material to be measured, the process conditions and the accuracy requirements. Here is a checklist that can help you choose the right interface measurement:
- Type of material:
Which material is to be measured (e.g. liquid, solid, gas)?
Are there any special properties of the material that need to be taken into account, such as viscosity, temperature, conductivity or density? - Measurement principle:
Which measuring principle is most suitable? (e.g. capacitive, radiometric, float, radar, etc.)
Does the measuring principle match the type of material and the process requirements? - Process conditions:
What temperature and pressure conditions prevail in the application?
Are aggressive chemicals or abrasive materials present that could affect the measuring probe? - Measuring range and accuracy:
What measuring range is required (e.g. minimum and maximum values)?
What accuracy and resolution are needed? - Mounting and installation conditions:
What kind of space is available?
Can the measuring probe be easily integrated into the process? - Output signals:
What type of output signals are required (e.g. 4-20 mA, HART, Modbus, analogue voltage)?
Can the measuring device be integrated into your existing control or monitoring systems? - Maintenance and cleaning:
Is regular maintenance necessary?
Can the measuring probe be easily cleaned or maintained? - Safety and certification requirements:
Are there any special safety requirements or certifications (e.g. ATEX, SIL, WHG) to be observed? - Costs and budget:
What budget is available for interface measurement?
Are long-term operating costs to be taken into account? - Experience and training:
Do you already have experience in dealing with certain measurement methods?
Is training or support required? - Availability and delivery time:
How quickly do you need the measuring solution?
Is the selected device or technology readily available?
The right choice of suitable measurement technology for interface measurement enables reliable and precise detection and monitoring of the interface between two different materials in your industrial applications.